OEM CNC Lathe Part Supplier: Your Key to Precision Engineering
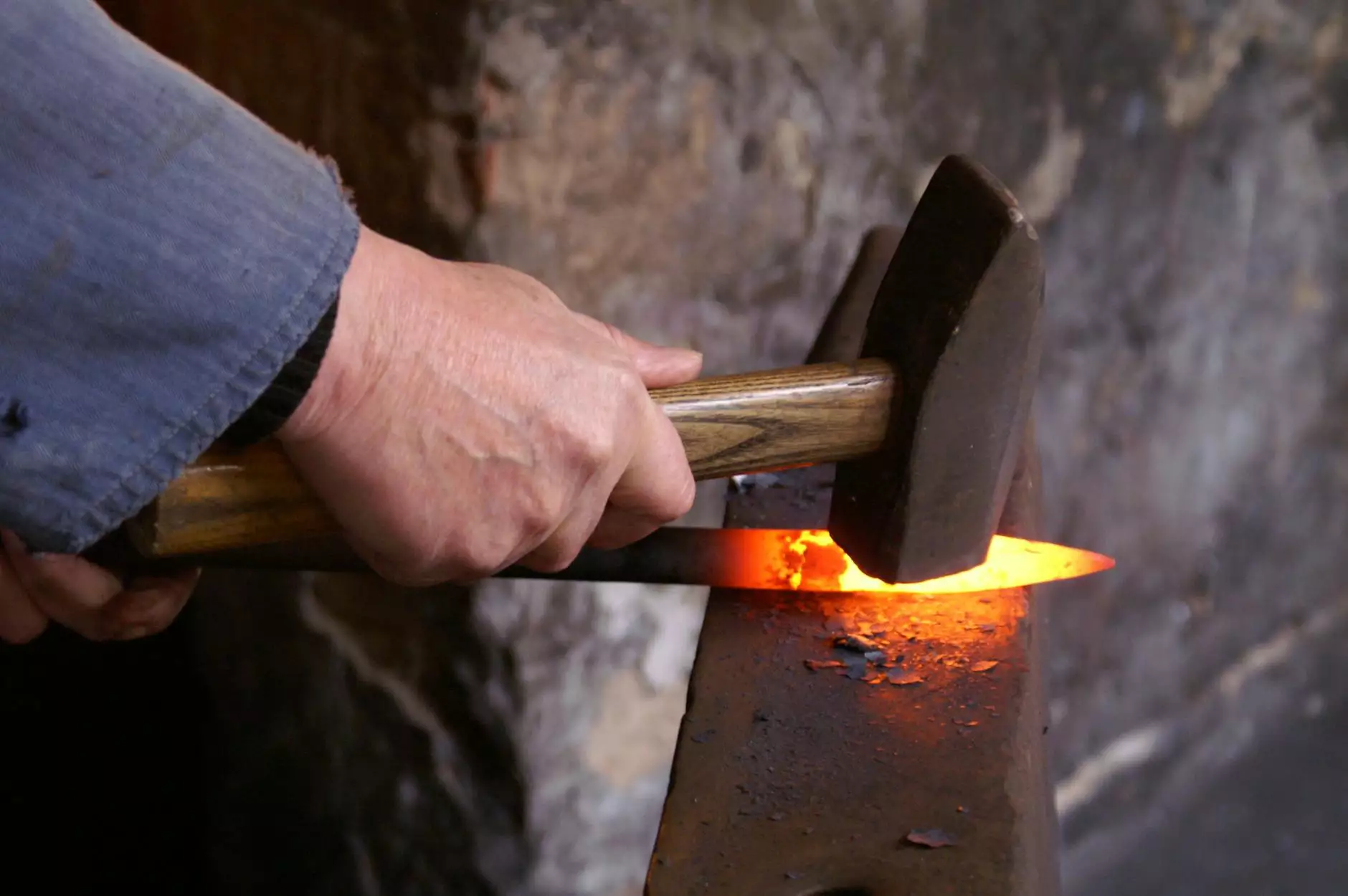
The manufacturing industry has seen remarkable advancements over the years. One of the pivotal technologies that have driven this transformation is the CNC (Computer Numerical Control) machining. Specifically, the role of an OEM CNC lathe part supplier cannot be overstated. As businesses seek to enhance operational efficiency and improve product quality, understanding the significance of these suppliers becomes essential.
Understanding CNC Machining and Its Importance
To truly appreciate the value of an OEM CNC lathe part supplier, it is vital to understand what CNC machining entails. CNC machining is a subtractive manufacturing process that uses computerized controls to manipulate machinery and tools to shape materials—most often metals and plastics—into desired forms.
Key Advantages of CNC Machining
- Precision: CNC machining boasts remarkably high levels of accuracy, allowing manufacturers to create parts with very tight tolerances.
- Efficiency: Automation reduces the time taken to produce parts, enabling faster turnaround and increased production rates.
- Flexibility: CNC machines can produce a wide variety of shapes and sizes, enabling manufacturers to meet diverse customer demands.
- Consistency: Once a design is programmed, CNC machines can produce identical parts consistently, ensuring uniformity.
The Essential Role of OEM CNC Lathe Part Suppliers
An OEM CNC lathe part supplier is specialized in producing lathe parts and components essential for various machining processes. These suppliers work with Original Equipment Manufacturers (OEMs) to ensure that the components they provide meet specific standards and requirements.
What Makes a Supplier Stand Out?
When choosing an OEM CNC lathe part supplier, various factors can influence your decision. Here are some crucial aspects that make a supplier trustworthy and reliable:
- Quality Assurance: The supplier should utilize stringent quality control processes to ensure that all components meet the necessary specifications.
- Material Expertise: A supplier with extensive knowledge of various materials—such as aluminum, steel, and titanium—can better advise on the ideal choices for your specific applications.
- Advanced Technology: Utilizing state-of-the-art CNC machinery and software enhances the precision and quality of the parts produced.
- Customization Capabilities: The ability to customize components to meet unique specifications is essential for many manufacturing processes.
- Timeliness: Fast production times and reliable delivery schedules are crucial for maintaining your business operations.
Benefits of Partnering with an OEM CNC Lathe Part Supplier
Integrating an OEM CNC lathe part supplier into your manufacturing process can yield various benefits that ultimately enhance your bottom line. Here are some advantages of establishing a partnership with these suppliers:
1. Cost Efficiency
Outsourcing your CNC lathe parts can significantly reduce manufacturing costs. By leveraging the supplier's existing resources, you can avoid investing in expensive machinery and skilled labor.
2. Access to Expertise
OEM CNC lathe part suppliers bring a wealth of experience to the table. Their expertise can guide your product development, ensuring that you achieve optimal results efficiently.
3. Scalability
As your business grows, your demand for precision parts may also increase. A reliable supplier can easily scale production capabilities to meet your changing needs.
4. Innovation
Many leading suppliers invest in research and development. Partnering with an innovative supplier can give you access to the latest technologies and production techniques.
Creating a Partnership with Your Supplier
Establishing a successful collaboration with your OEM CNC lathe part supplier is imperative for ensuring a seamless manufacturing workflow. Here are key steps to foster this partnership:
1. Clear Communication
Open lines of communication are crucial for a successful partnership. Clearly articulate your requirements and expectations from the outset.
2. Define Your Needs
Provide detailed specifications for the parts you require. Working together to ensure that the supplier understands your designs will lead to better outcomes.
3. Routine Reviews
Schedule regular meetings to discuss project progress, feedback, and any challenges that may arise. This continuous feedback loop ensures that both parties are aligned.
Quality Control Measures
Quality is paramount when it comes to CNC machining. An effective OEM CNC lathe part supplier maintains several quality control measures to ensure the parts produced meet high standards.
1. Inspection Procedures
Implement rigorous inspection protocols to check the dimensions and specifications of parts throughout the manufacturing process.
2. Certifications and Standards
Verify that the supplier complies with industry standards such as ISO 9001, which guarantees adherence to international quality management systems.
3. Feedback Mechanisms
Encourage honest feedback from your supplier about design and production processes to identify potential areas for improvement.
Conclusion: The Future of CNC Machining
The role of an OEM CNC lathe part supplier is vital in today’s competitive manufacturing landscape. By partnering with an experienced and skilled supplier, businesses can enhance production efficiency, improve product quality, and adapt to market demands. As technologies continue to evolve, staying ahead of these advancements through strong vendor relationships will be integral to your business's success.
If your business is in need of high-quality lathe parts, consider reaching out to deepmould.net. Our commitment to precision engineering and customer satisfaction makes us your ideal OEM CNC lathe part supplier. Together, we can ensure your manufacturing processes are not only efficient but also competitive in today’s marketplace.